Оригинальная ссылка кракен браузера
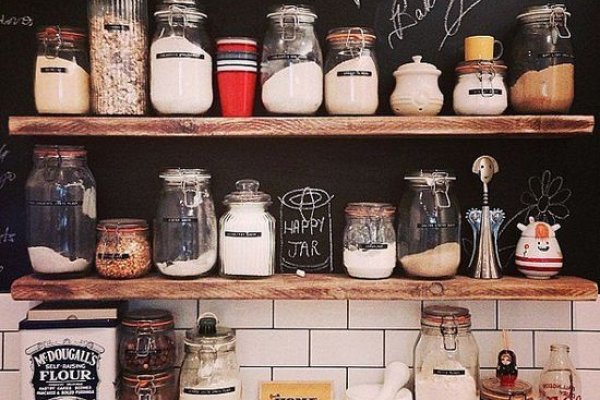
Всегда читайте отзывы и будьте в курсе самого нового, иначе можно старь жертвой обмана. Товары и услуги, продающиеся на даркнете: Нетипичные инструкции Именно так можно назвать инструкции, которые можно найти на сайтах даркнет. Спецслужбы Ещё одной - и, пожалуй, главной - проблемой сети Tor являются спецслужбы. Периодически, чаще всего во время весеннего или осеннего обострения они устраивают «крестовые походы пытаясь «очистить мир от скверны». Уже кракен само название сети даркнет можно расшифровать как что-то темное или же даже скрытое. Любой желающий может внести человека в список или повысить ставку по уже существующим позициям. Юзать с Тором браузеры типа Chrome от Google, Яндекса, etc. Будь к этому готов. Затем распакованную папку можно перетаскивать куда угодно и оттуда запускать. А то снег башка попадёт - совсем мёртвый будешь» «Джентльмены удачи». И абсолютно наплевать, с какой целью он это делает, благие или нет у него намерения. Ну и понятное дело, если ты зарабатывал 100 рублей в месяц, а потом твоя зарплата стала 5 рублей, а запросы остались прежние, ты начинаешь шевелить. Статья 222 УК РФ штраф до 200 тыс. Их мало. Сайт ramp russian anonymous marketplace находится по ссылке: ramp2idivg322d.onion. Заражённые файлы К хакерам вплотную примыкает проблема с заражёнными файлами самого Tor Browser-а. Также в этой сети встречаются различные отморозки, откровенные шизоиды, маньяки и прочие уроды. Советую на этой вкладке обратить внимание на ссылку «Проверка интернет-настроек Tor». Http k4bmdpobhqdguh2y.onion/ - блог о новых скрытых сервисах сети (ENG). Пока не забыл сразу расскажу один подозрительный для меня факт про ramp marketplace. Да и кто сказал, что в следующий раз они ограничатся только этим? А на десерт небольшой список «луковых» сайтов, так сказать, для разгона. И даже на многих иноговорящих форумах появляются разделы для русских. По слухам основной партнер и поставщик, а так же основная часть магазинов переехала на торговую биржу. Не терпится поскорее поставить и попробовать это чудо? Флибуста (http flibustahezeous3.onion - зеркало знаменитой библиотеки в «луковой» сети (язык RU).
Оригинальная ссылка кракен браузера - Кракен маркетплейс kr2web in площадка торговая
н. Минфин США ввело против него санкции. Потребитель не всегда находит товар по причине того что он пожалел своих денег и приобрел товар у малоизвестного, не проверенного продавца, либо же, что не редко встречается, попросту был не внимательным при поиске своего клада. Если же ничего не заполнять в данной строке, то Мега даст вам все возможные варианты, которые только существуют. Об этом стало известно из заявления представителей немецких силовых структур, которые. Небольшой список.onion сайтов в сети Tor. Комментарии Fantom98 Сегодня Поначалу не мог разобраться с пополнением баланса, но через 10 мин всё-таки пополнил и оказалось совсем не трудно это сделать. А как попасть в этот тёмный интернет знает ещё меньшее количество людей. Onion - Checker простенький сервис проверки доступности.onion URLов, проект от админчика Годнотабы. Оплата за товары и услуги принимается также в криптовалюте, как и на Гидре, а конкретнее в биткоинах. Pastebin / Записки Pastebin / Записки cryptorffquolzz6.onion - CrypTor одноразовые записки. Onion - Onion Недорогой и секурный луковый хостинг, можно сразу купить onion домен. Отдельного внимания стоит выбор: Любой, моментальный, предварительный заказ или только надёжный. Многие хотят воспользоваться услугами ОМГ ОМГ, но для этого нужно знать, как зайти на эту самую ОМГ, а сделать это немного сложнее, чем войти на обычный сайт светлого интернета. Onion - Продажа сайтов и обменников в TOR Изготовление и продажа сайтов и обменников в сети TOR. Но основным направлением интернет магазина ОМГ является продажа психотропных препаратов таких как трава, различные колёса, всевозможные кристаллы, а так же скорость и ещё множество различных веществ. На тот момент ramp насчитывал 14 000 активных пользователей. История посещений, действий и просмотров не отслеживается, сам же пользователь почти постоянно может оставаться анонимом. Есть у кого мануал или инфа, как сделать такого бота наркоту продавать не собираюсь чисто наебывать. График показывает динамику роста внешних ссылок на этот сайт по дням. Независимый архив magnet-ссылок casesvrcgem4gnb5.onion - Cases. Sblib3fk2gryb46d.onion - Словесный богатырь, книги. Onion - SkriitnoChan Просто борда в торе. Хостинг изображений, сайтов и прочего Tor. Hbooruahi4zr2h73.onion - Hiddenbooru Коллекция картинок по типу Danbooru. Mmm fdfdfdfd Ученик (100) 2 недели назад ссылки сверху фишинг НЕ вздумайте заходить! Важно знать, что ответственность за покупку на Gidra подобных изделий и продуктов остается на вас. То есть вы можете прийти со своим обычным кошельком зарегистрированные на вас же и купив определенные монета, а после их продав вы получаете дополнительные транзакции и конвертацию средств. Возможность создавать псевдонимы. Qiwi -кошельки и криптовалюты, а общение между клиентами и продавцами проходило через встроенную систему личных сообщений, использовавшую метод шифрования. Onion/ - Blockchain пожалуй единственный онлайн bitcoin-кошелек, которому можно было бы доверить свои монетки. Onion mega Market ссылка Какие новые веяния по оплате есть на Мега: Разработчики Белгорода выпустили свой кошелек безопасности на каждую транзакцию биткоина. Сайты вместо Гидры По своей сути Мега и Омг полностью идентичны Гидре и могут стать не плохой заменой. Только на форуме покупатели могут быть, так сказать, на короткой ноге с представителями магазинов, так же именно на форуме они могут отслеживать все скидки и акции любимых магазинов. Часто сайт маркетплейса заблокирован в РФ или даже в СНГ, поэтому используют обходные зеркала для входа, которые есть на нашем сайте. Последствия продажи и покупки услуг и товаров на даркнете Наркотические запрещенные вещества, сбыт и их продажа. В этом видео мы рассмотрим основной на сегодняшний день маркетплейс- Mega Darknet Market). Сохраненные треды с сайтов.

Кларнеты Евгений Бархатов, Игнат Красиков. 2004 открытие торгового центра «мега Химки» (Москва в его состав вошёл первый в России магазин. Поиск по карте Находи и покупай клады прямо на карте. Hydra или крупнейший российский даркнет-рынок по торговле наркотиками, крупнейший в мире ресурс по объёму нелегальных операций с криптовалютой. Наша матанга http matangapatoo7b4vduaj7pd5rcbzfdk6slrlu6borvxawulquqmdswyd onion market 6688, matanga union ссылка тор matanga2planet com, matanga matanga2original. Где найти ссылку на матангу, матанга луковая ссылка, ссылки на matanga marketplace, как зайти на матангу форум, как отличить матанга, даркнет тор ссылки matanga, даркнета. Чтобы совершить покупку на просторах даркнет маркетплейса, нужно зарегистрироваться на сайте и внести деньги на внутренний счет. В 2015 финансовом году (с 1 сентября 2014 года по года) торговые центры мега в России посетили 275 миллионов человек. Похожие каналы. Это не полный список кидал! Onion - Anoninbox платный и качественный e-mail сервис, есть возможность писать в onion и клирнет ящики ваших собеседников scryptmaildniwm6.onion - ScryptMail есть встроенная система PGP. Отдельного внимания стоит выбор: Любой, моментальный, предварительный заказ или только надёжный. Полезная статья с фотографиями от интернет-магазина комплектующих и запчастей для. Для того чтобы войти на рынок ОМГ ОМГ есть несколько способов. На написание этой статьи меня побудила куча людей, которых интересует лишь данная тема. Russian Anonymous Marketplace один из крупнейших русскоязычных теневых форумов и торговая площадка. Оригинал сайт рабочая ссылка. Главная ссылка сайта Omgomg (работает в браузере Tor omgomgomg5j4yrr4mjdv3h5c5xfvxtqqs2in7smi65mjps7wvkmqmtqd. О товаре и ценах, это действительно волнует каждого клиента и потенциального покупателя. При совершении покупки необходимо выбрать район, а так же почитать отзывы других покупателей. Проект существовал с 2012 по 2017 годы. Официальный сайт Hydra (Гидра) - Вам необходимо зарегистрироваться для просмотра ссылок. Avel - надежный сервис по продаже авиабилетов. Группа СберМегаМаркет в Одноклассниках. Правильная ссылка на! Маркетплейс СберМегаМаркет каталог товаров интернет-магазинов. Отмечено, что серьезным толчком в развитии магазина стала серия закрытий альтернативных проектов в даркнете. Реестр новостных агрегаторов. По размещенным на этой странице OMG! Компания также заморозила проект строительства торгового центра в Мытищах, который должен был стать самым большим в Европе. RAM 1500 - Автосалон Ramtruck. @onionsite_bot Бот. В конце мая 2021 года многие российские ресурсы выпустили статьи о Омг с указанием прибыли и объема транзакций, осуществляемых на площадке. Всегда свежая на ОМГ! Они не смогут скрываться в даркнете или на форумах, они не смогут скрываться в России или где-то в других странах сказано в заявлении Минфина. «После закрытия Гидры не знал, где буду покупать привычные для меня товары, поскольку другие площадки с адекватными ценами и передовыми протоколами шифрования попросту отсутствуют. Onion/?x1 - runion форум, есть что почитать vvvvvvvv766nz273.onion - НС форум. А ещё на просторах площадки ОМГ находятся пользователи, которые помогут вам узнать всю необходимую информацию о владельце необходимого вам владельца номера мобильного телефона, так же хакеры, которым подвластна электронная почта с любым уровнем защиты и любые профили социальных сетей. Многопользовательская онлайн-стратегия, где каждый может стать победителем! Источник p?titleМега сеть_торговых_центров) oldid. Для Android. Она специализировалась на продаже наркотиков и другого криминала. Попробовал.